Designing the Steel E-Motive autonomous vehicle concepts required our team of engineers to rethink everything from the ground up. We had a choice: modify a conventional vehicle or start with a clean sheet. We chose the latter, which led to several innovations, some of which could readily be applied to today’s vehicles.
Why Clean Sheet Design?
Starting with a clean sheet approach allowed us to address and encompass the unique opportunities of designing an autonomous vehicle. Assuming a conventional/existing vehicle design as the basis for the Steel E-Motive concept, we might have carried over compromises inherent in vehicles designed for human drivers. By starting fresh, we could rethink the entire design process and optimize every aspect of the vehicle for autonomy.
Present-day passenger vehicle designs center around the driver – their seating position and location of key features, including steering wheel, pedals, and visibility requirements. These constraints are removed with an autonomous vehicle design, so having this freedom allowed us to explore new seating configurations and interior layouts, providing improved comfort and better use of space for the passengers.
The seating orientation can be significantly more flexible without a driver, so we placed the passengers facing each other. Users are more comfortable face-to-face, especially when sharing rides with strangers. This configuration enhances comfort and addresses personal space issues, making the journey more pleasant for riders.
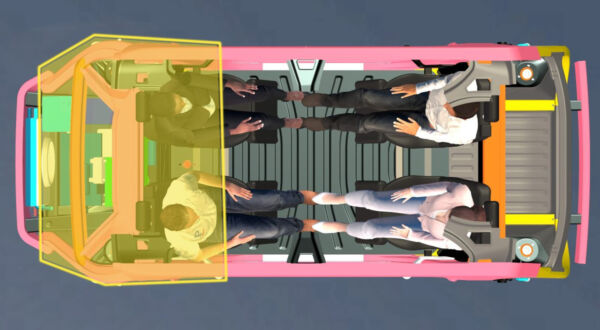
In Mobility-as-a-Service vehicles, consumers feel more comfortable facing other occupants than in other seating arrangements.
Safety Innovations for Autonomous Vehicles
Safety was a critical element of Steel E-Motive’s design requirements. One of the most significant challenges was developing effective crash protection systems. Since front-row rear-facing passengers are potentially more vulnerable in a frontal collision than conventional seating positions, we needed to rethink the approach to collision management and protection for autonomous vehicles like robotaxis.
Our solution was the design of front, side, and rear crash structures that performed exceptionally well for our autonomous vehicle and potentially for conventional vehicles. To achieve that, we used 3D structural topology optimization methods to identify the key load paths for the body structure. Protection of occupants in their unique locations was achieved by using Ultra-High-Strength Steels, such as Press-Hardened and Martensitic grades, in the body structure around the occupants.
The Frontal Impact Glance-Off Beam
The glance-off beam is one of the key elements of the Steel E-Motive front crash structure. It helps to guide and deflect the vehicle along the IIHS small overlap rigid barrier during frontal impact whilst folding and crushing in frontal rigid and offset deformable barrier tests. This results in a lower crash pulse and intrusion levels, reducing the risk of serious injury to the occupants and damage to the propulsion battery. The Press-Hardened grade of Advanced High-Strength Steel – when combined with the glance-off beam geometry and profile – enables the Steel E-Motive concept design to achieve very good frontal crash performance.

The Small Offset Crash Glance Beam is an industry first. It is designed to minimize cabin intrusion and lower the crash pulse, minimizing occupant injury.
Side Impact Hex Beam
Another important innovation was the development of a side-crash hex beam. This Advanced High-Strength Steel component is designed to provide controlled crush and collapse of the rocker profile in a side impact. Two roll-formed Dual Phase grade sheets are spot-welded to form several crush-can-like hexagonal-shaped profiles perpendicular to the impact direction. The Dual Phase AHSS properties and edge/corner profile of the hex beam deliver a high degree of energy absorption, contributing to the overall protection of the occupants and battery in a side-impact collision.
The hex beam’s design resulted from extensive simulation and testing. By leveraging advanced steels and manufacturing techniques, we created a component that offers superior performance without adding significant weight to the vehicle.
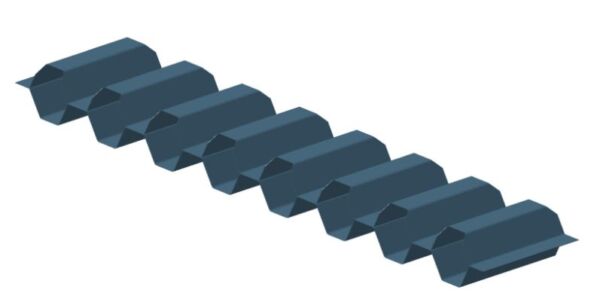
Hex beam energy absorbers are low-cost, compact, and mass-efficient, minimizing side crash intrusion and achieving superior battery protection.
Technological Advances Assist Design Engineering
We also embraced utilizing new technology during the design process. One of the most exciting developments was using virtual reality (VR) for structural load path analysis and visualization of crash simulation results. Visualizing crash load paths and simulation results in 3D allowed us to optimize the material placement and structural design. This innovative approach helped us achieve superior safety performance and demonstrated the incredible potential of VR in automotive engineering.
Conclusion
Ultimately, starting with a clean sheet for the Steel E-Motive autonomous vehicle design was the right decision. It allowed us to rethink every aspect of the vehicle, from interior layout to safety systems, and to embrace new ideas and technologies that enhanced our design process. The results speak for themselves: Steel E-Motive vehicle concepts, optimized for autonomy, provide superior safety and comfort for passengers.